INJECTION MOLDING
Experienced Capability.
Exceptional Craftsmanship.
Mastery in every mold.
Precision Plastics for Mission Critical Parts
High-performance injection molding demands a scientific approach. We use Scientific Injection Molding (SIM) to ensure every part meets the strictest standards for precision, repeatability, and compliance. Whether you’re manufacturing medical devices, aerospace components, or critical industrial parts, our data-driven process eliminates variation and maximizes quality.
Our overmolding process allows us to combine multiple materials into a single component, enhancing functionality and performance. This process is ideal for creating ergonomic designs and improving the durability of parts. We use cutting-edge technology to ensure a seamless bond between materials, resulting in superior end products.
Insert molding integrates metal or plastic inserts into the molded parts during the injection process. This technique enhances the strength and functionality of components, making it perfect for complex assemblies. Our expertise in insert molding allows us to produce parts with embedded reinforcements, electrical components, or threaded inserts with precision.
We offer specialized medical molding services to produce high-precision, sterile components for the healthcare industry. Our Class 8 Clean Room ensures that all medical parts are manufactured in a controlled, contamination-free environment. This guarantees the highest standards of cleanliness and compliance with medical regulations.
Micro injection molding is a technique for producing tiny and precise components using minimal resin volumes in the injection procedure. Our expertise in micro injection molding allows us to create intricate parts with high accuracy, perfect for industries such as medical devices, electronics, and automotive components.
Injection Molding Ancillary Services

Prototypes to Production at Scale
Our injection molding services cater to small quantity prototypes, as well as full-scale production. Whether you need a few test pieces or millions of units, we have the capability to meet your demands efficiently.

Tool Transfer
We have a defined project management and quality assurance process for intaking tools from other manufacturers. Our team can repair and modify existing tools to get your production back on track quickly.

Post-Processing and Assembly
Our secondary operations include machining, bonding, and finishing. We can also offer assembly and packaging in our Class 8 Clean Room, maintaining the highest standards of cleanliness and quality.
From Concept to Production
From first concept to full-scale production, every molded part follows a path. We guide you through each stage—Design for Manufacturability (DFM), Prototype Tooling, Bridge Tooling, and Production Tooling—so your part is optimized for performance, cost, and scalability at every step.
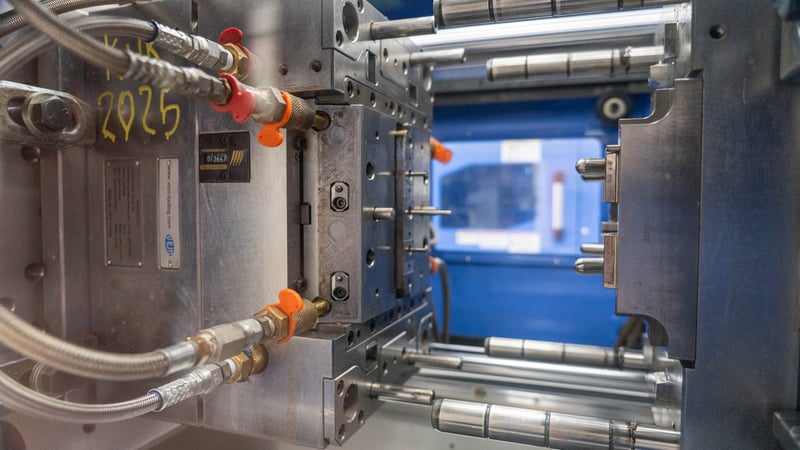
Injection Molding Lifecycle Timeline
-
Design for Manufacturability (DFM)
This is where it all begins. We collaborate with you to refine your part design, reduce risk, and ensure it’s moldable, manufacturable, and cost-effective. Good DFM sets the foundation for success.
-
Prototype Tooling
A low-investment mold that helps you test your part in real-world materials and get early feedback. It’s essential for validating design intent and function before locking in production details.
-
Bridge Tooling
Perfect for short-run production or when demand is ramping up. This stage fills the gap between prototyping and full-scale tooling—giving you molded parts faster while final production tooling is underway.
-
Production Tooling
Your long-term tool built for repeatability, efficiency, and high-volume output. This is where consistency, cycle time, and quality control really matter—and where all the upfront planning pays off.
By incorporating these considerations into your design, we ensure a more efficient injection molding process, leading to high-quality, cost-effective parts.
Why Trust Aprios with your Injection Molding Needs
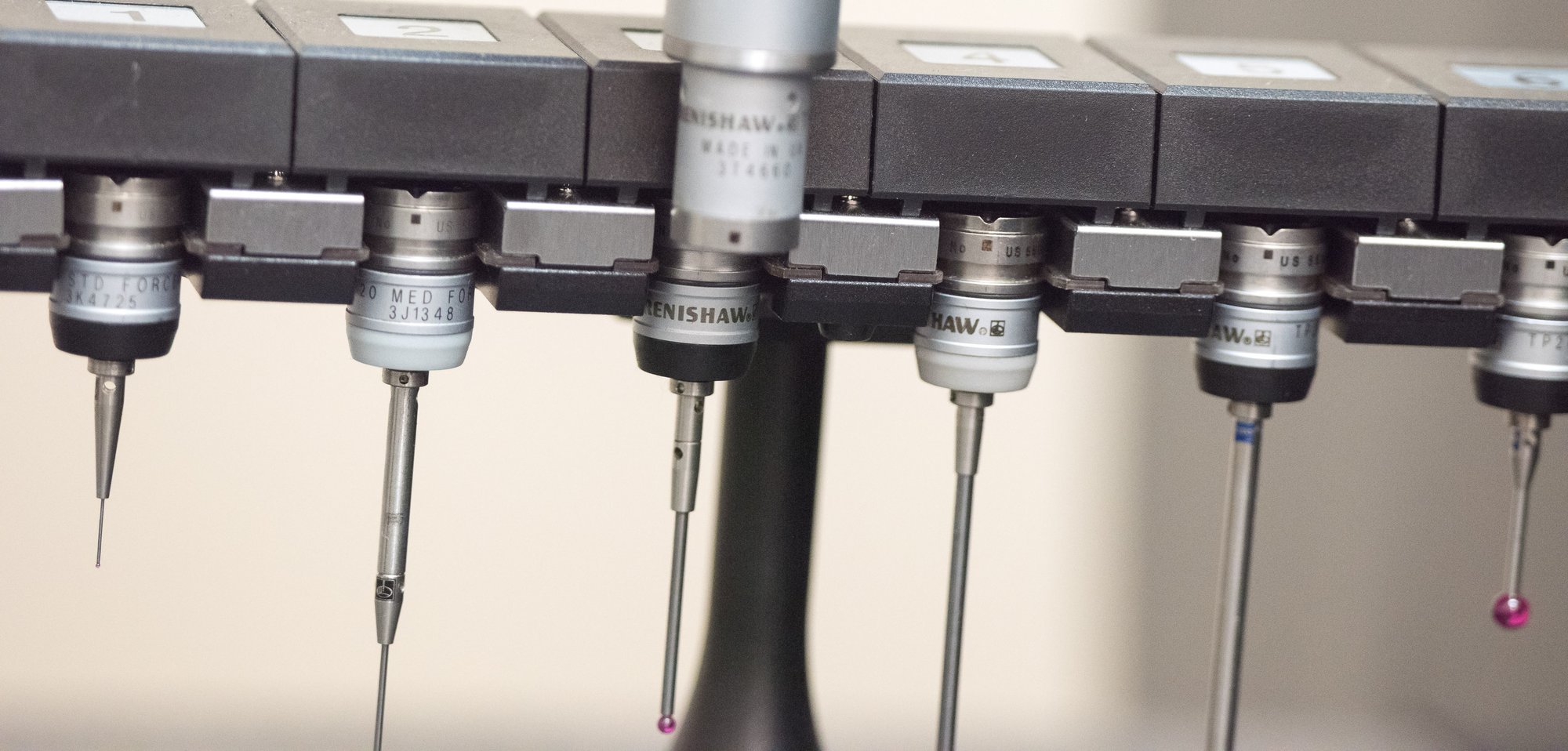
Quality Assurance and Compliance
We adhere to stringent quality assurance protocols and comply with industry standards to ensure the reliability of every part we produce. Our comprehensive testing and inspection processes guarantee that each component meets your exact specifications. For more information, please visit our Quality page. This commitment to quality reduces the risk of defects and enhances the overall performance of your products.
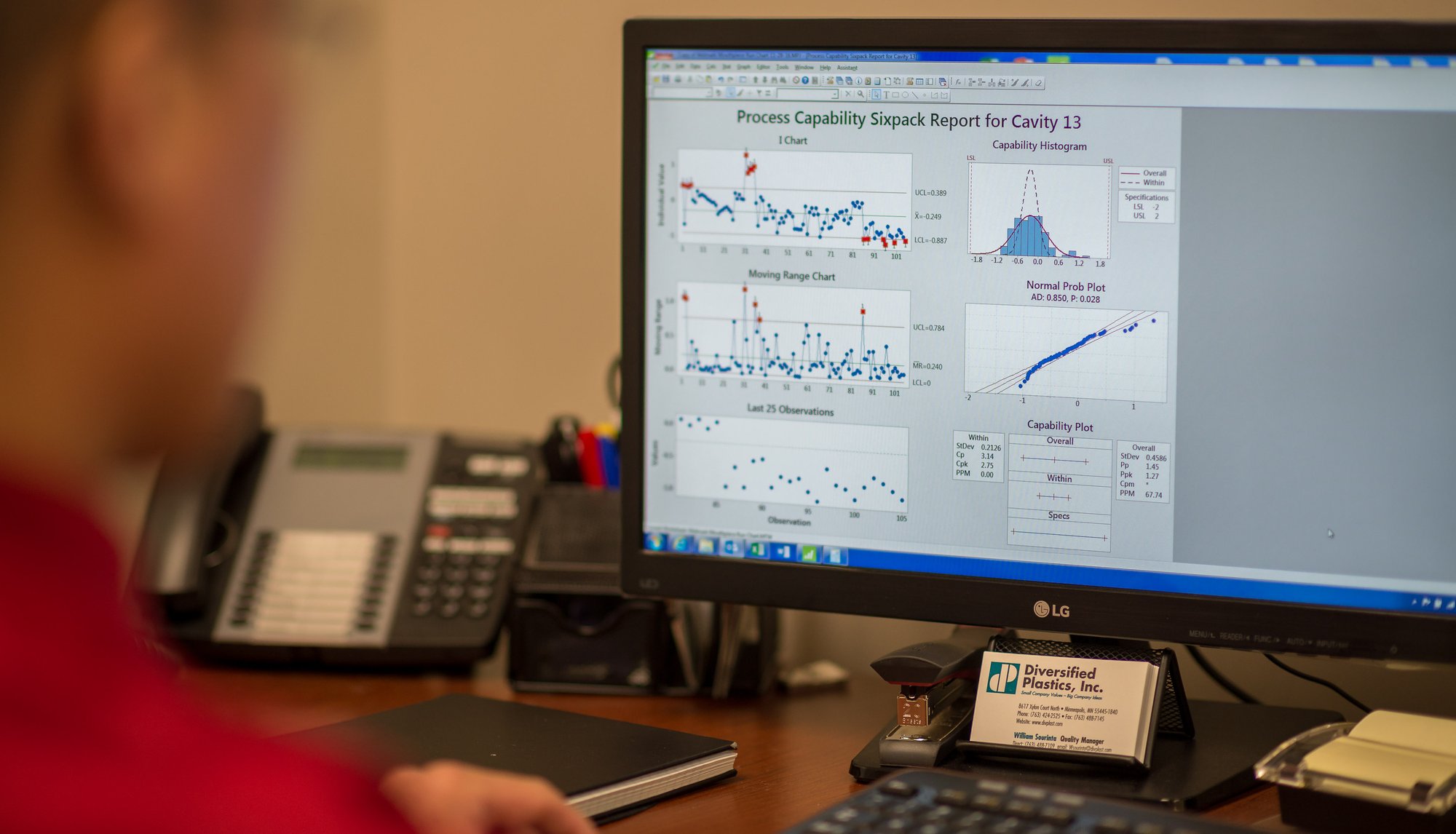
Design for Manufacturing (DFM)
Our Design for Manufacturing (DFM) services help you optimize your designs for efficient and cost-effective production. By collaborating early in the design process, we identify potential issues and suggest improvements to enhance manufacturability. This proactive approach reduces time-to-market, lowers production costs, and ensures that your products are designed with manufacturing efficiency in mind.

Quick-Turn Tooling
We understand the importance of speed in bringing new products to market. Our quick-turn tooling services enable us to deliver parts within a month after placing an order. This rapid turnaround time allows you to accelerate your product development cycles and respond swiftly to market demands, giving you a competitive edge.
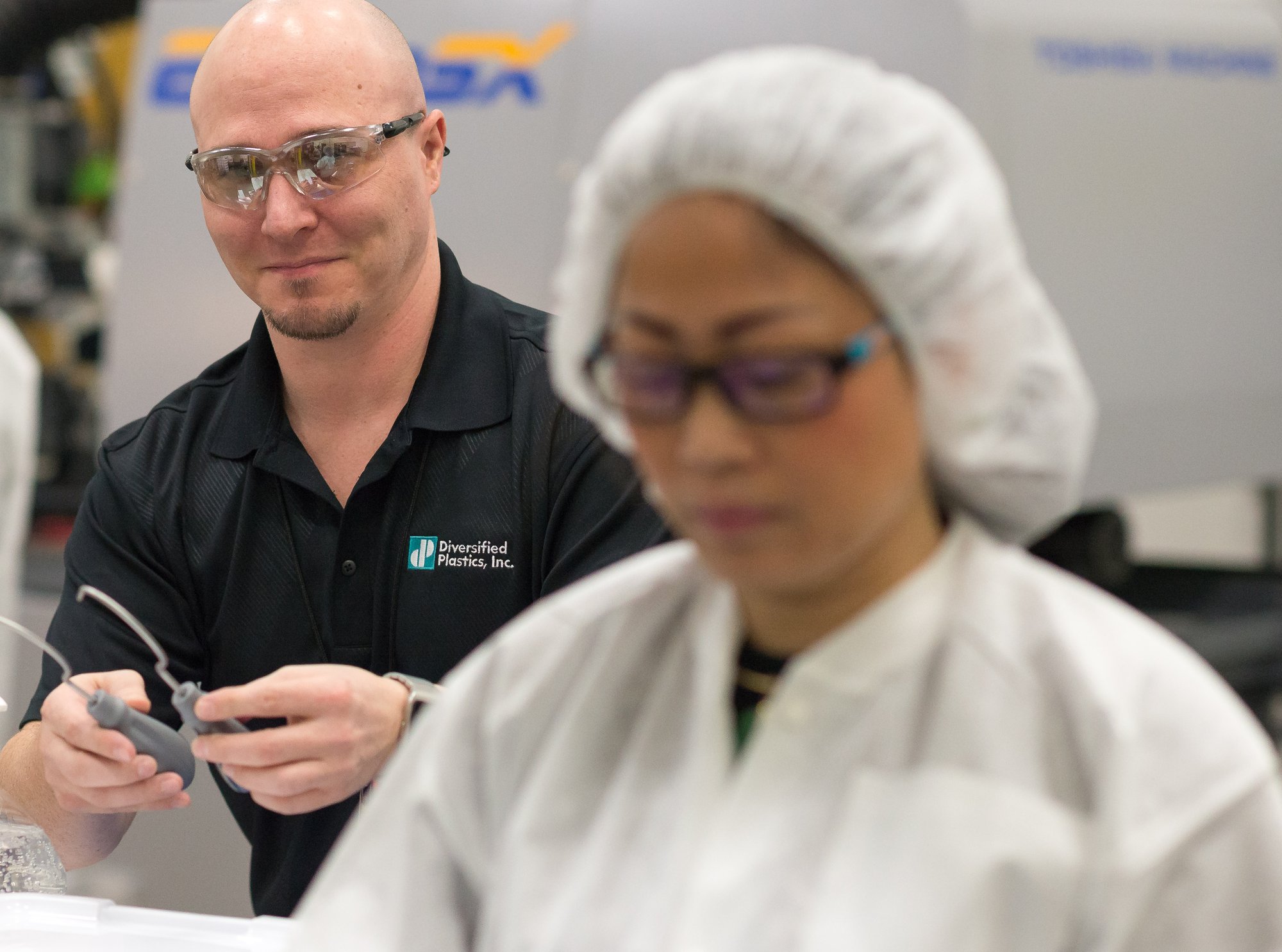
Partnership and Support
We view our clients as partners and are dedicated to supporting your success from concept to completion. Our experienced team is available to assist with design, prototyping, production, and post-production services. This end-to-end support ensures a smooth and successful project execution, allowing you to focus on your core business objectives.
Frequently Asked Questions
-
What types of materials can you use for injection molding?
We can work with a wide range of thermoplastic materials, including ABS, polycarbonate, polyethylene, polypropylene, and more. We select materials based on your specific application requirements, such as strength, flexibility, and temperature resistance. We do not work with PVC or Teflon.
-
What are the benefits of overmolding and insert molding?
The overmolding process enhances the functionality and aesthetics of a product by combining different materials, such as a rigid plastic with a soft-touch surface. Insert molding integrates metal or plastic inserts into the molded parts, increasing strength and functionality, and is ideal for creating complex assemblies.
-
Can you handle small and large production runs?
Yes, we have the capability to manage both small quantity prototypes and large-scale production runs. Our flexible manufacturing processes ensure high-quality production regardless of the order size.
-
What are the build size limitations for your injection molding services?
We can handle parts with surface areas up to 156 square inches in the direction of the mold clamp. Specific dimensions like 10x15 or 12x13, and shot weights up to 61 ounces (3.8 pounds), are within our capacity.
-
How do you ensure the quality of injection molded parts?
We adhere to strict quality control processes, including comprehensive testing and inspection at various stages of production. Our commitment to quality ensures that each part meets your exact specifications and industry standards.
Need Top-Quality Injection Molding?
3 min read
Injection Molding Defects: Discoloration – Why It Happens and How to Avoid It
Mar 7, 2025 by Nick Erickson
2 min read
Guide to Optimal Material Choices for Injection Molding
Feb 20, 2025 by Nick Erickson
DFM in Plastic Injection Molding: Practical Design Tips for Better Parts
A quick-start guide for engineers designing smarter, more manufacturable plastic parts.
WHAT'S INSIDE:
- Draft angles, wall thickness, and parting line best practices
- How to avoid common pitfalls like sink, warping, and knit lines
- Tooling design insights: gating, venting, and mold flow
- Rib, boss, and corner radius guidelines
- How mold flow analysis helps you get it right the first time