2 min read
Rapid Response: Addressing Medical Device Challenges for Diabetes Care
Nick Erickson : Feb 28, 2025 10:56:17 AM
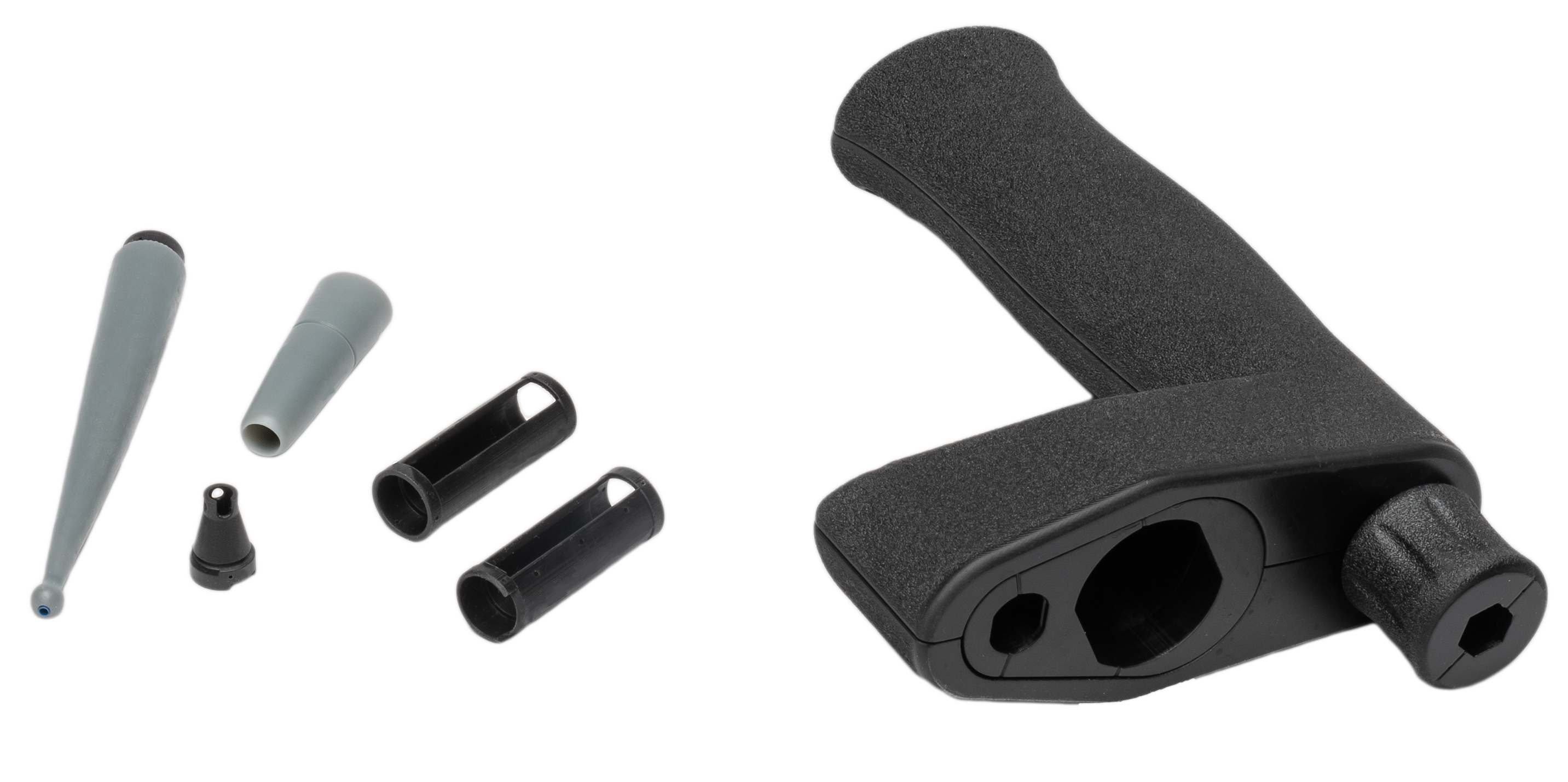
Introduction
In response to the escalating diabetes crisis, we partnered with a client specializing in medical devices to expedite the development and market introduction of a groundbreaking endoscopic treatment. Our objective was to address severe complications associated with type 2 diabetes while managing budget constraints and minimizing the project timeline.
Project Background
The project focused on developing a novel catheter for managing type 2 diabetes complications in response to the growing health crisis. With approximately 34 million Americans diagnosed with diabetes, the need for innovative medical solutions is urgent. The partnership aimed to streamline the traditional lengthy development process, enabling efficient market introduction while adhering to budget constraints.
By leveraging advanced manufacturing techniques and rapid prototyping, the collaboration sought to meet strict safety and performance standards, ultimately setting new benchmarks for speed and efficiency in medical device development.
Supplier Selection
Our engagement began with thorough consultations to understand the specific needs and constraints of the device. We focused on gathering requirements related to mechanical properties, safety standards, and performance metrics, ensuring all critical aspects were considered from the outset.
“Working with Aprios allowed us to produce multiple design iterations at a rapid pace, saving vital time – a crucial factor for startups.
- Research and Development Engineer
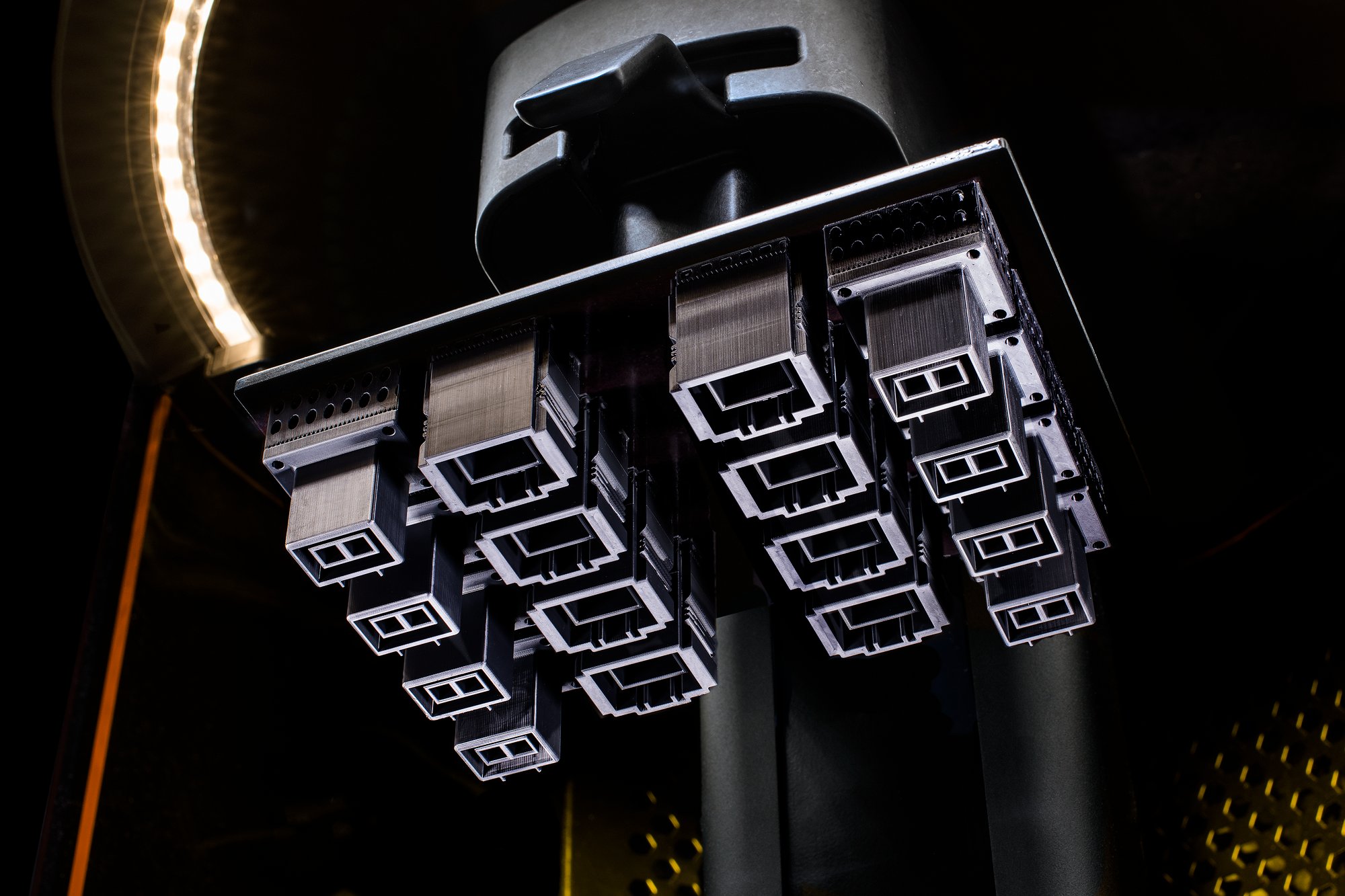
Technical Enhancements
-
DESIGN FOR MANUFACTURING (DFM)
We conducted iteration cycles that facilitated continuous testing and feedback from the client, ensuring real-time improvements -
MATERIAL SELECTION
RPU 70, SIL 30, and RPU 130 were chosen for their strength, flexibility, and durability, respectively, addressing the needs of various components. -
OPTIMIZED FEATURES
We incorporated internal supports and vent holes to enhance aesthetics and cleanability, while threaded features ensured easy assembly.
Manufacturing Processes
-
INITIAL CONSULTATION Gathering comprehensive requirements related to mechanical properties, safety standards, and performance metrics to ensure all critical aspects were considered from the outset.
-
ITERATION CYCLES Rapid production of prototypes for continuous testing and feedback, allowing for real-time improvements based on client input.
-
FEATURE IMPROVEMENTS Incorporating ergonomic and functional enhancements, such as textured surfaces for better grip.
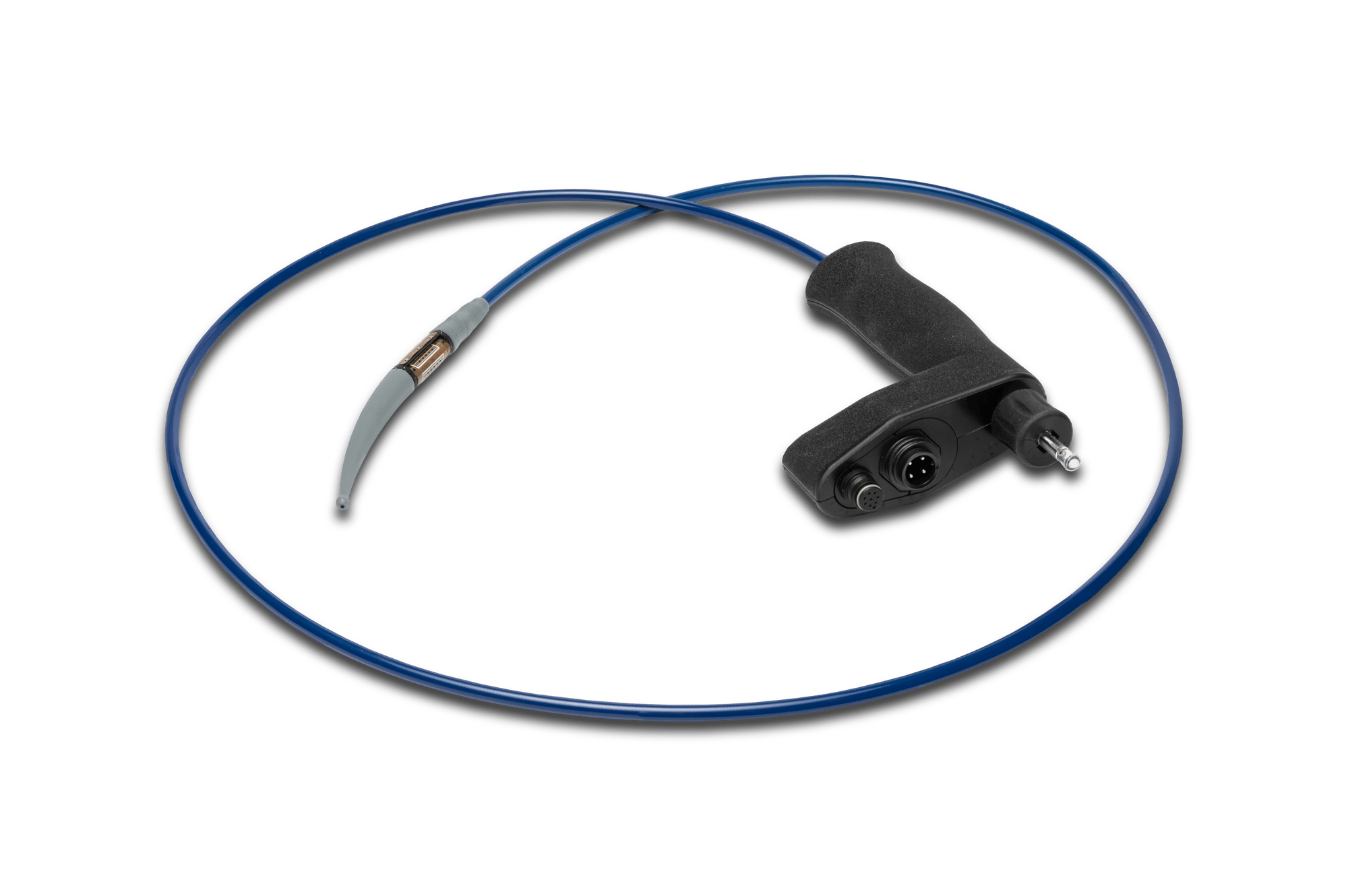
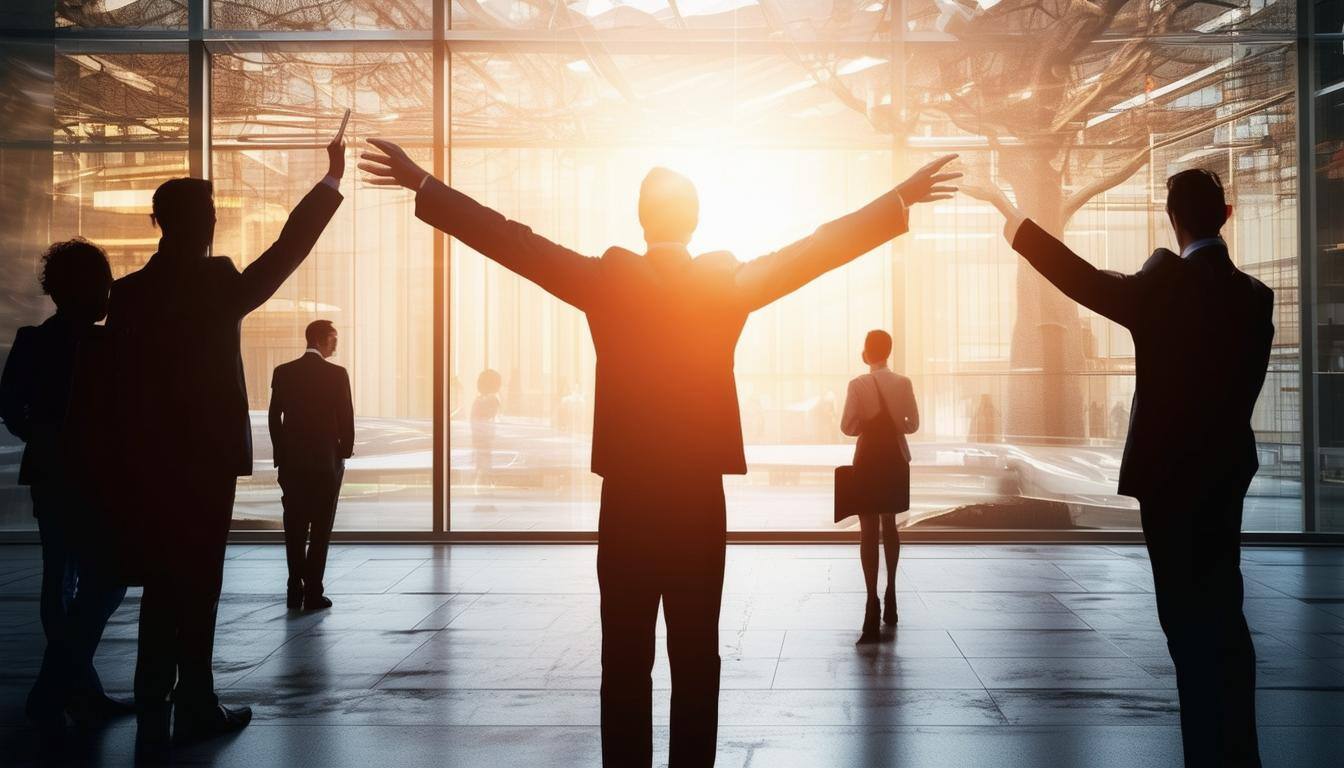
Results
ACCELERATED PRODUCT DEVELOPMENT
Through the use of rapid prototyping and additive manufacturing, we drastically reduced the development cycle time. A prototype was created in less than 24 hours, enabling swift iterations and continuous testing.COST EFFICIENCY
By optimizing the development and testing phases, we saved millions of dollars. This optimization prevented the need for the client to raise additional capital. Our streamlined process not only conserved financial resources but also expedited the pathway to clinical trials, a critical phase in medical device approval.
Future Outlook
With a potential second wave of COVID-19 on the horizon, Aprios is proactively investing in additional presses to ensure they can continue to meet global demand. Their commitment to being prepared reflects a caring approach to healthcare needs.
Conclusion
Through our collaborative efforts, we demonstrated the power of innovative manufacturing techniques in overcoming complex challenges, achieving both financial and time efficiencies while delivering a superior product. For further inquiries, please contact us to discuss how our innovative solutions can meet your needs